Rollout wheel welding is a fascinating process that has transformed the manufacturing world. It’s not just about joining metals; it’s an art form that combines precision, engineering, and innovation. If you’ve ever wondered how those seamless wheels on your car or machinery are made, then you’re in the right place. This guide will dive deep into the world of rollout wheel welding, exploring its techniques, benefits, and applications.
Now, let’s be honest here. When you hear “welding,” the first thing that comes to mind might be sparks flying and big machines doing their thing. But rollout wheel welding? That’s a whole different ball game. It’s a specialized process that focuses on creating strong, durable, and aesthetically pleasing wheels. From industrial equipment to high-performance vehicles, this technique plays a crucial role.
Whether you’re a professional engineer, a DIY enthusiast, or simply curious about the mechanics behind wheel production, this article will provide you with all the info you need. Stick around, and let’s roll out some knowledge!
- Unlocking The Secrets Of Oslashmacroslashsectugravehellipugravefrac34oslashsup2oslashacuteuacutecopyucircoelig Ugravehellipugravedaggeroslashplusmnoslashacuteugravedaggeroslashplusmn A Journey Through Culture And Meaning
- Discover The Charm Of The Leo Cottage Union Pier Your Ultimate Lakeshore Retreat
Table of Contents
- Introduction to Rollout Wheel Welding
- A Brief History of Rollout Wheel Welding
- The Rollout Wheel Welding Process
- Tools and Equipment Needed
- Benefits of Rollout Wheel Welding
- Applications in Various Industries
- Tips for Successful Rollout Wheel Welding
- Common Challenges and Solutions
- Comparison with Other Welding Techniques
- The Future of Rollout Wheel Welding
Introduction to Rollout Wheel Welding
Alright, let’s kick things off by breaking down what rollout wheel welding actually is. Simply put, it’s a welding method used to join metal components to create wheels. Think of it as the glue that holds everything together, but instead of glue, we’re talking about intense heat and skill. The process involves heating metal parts to their melting point and fusing them together, creating a seamless and sturdy connection.
One of the coolest things about rollout wheel welding is its versatility. It’s not limited to just one type of wheel or material. From aluminum alloy wheels for cars to heavy-duty steel wheels for industrial machinery, this technique can handle it all. Plus, it offers a level of precision that other welding methods struggle to match.
Now, let’s talk numbers. According to recent studies, the global welding market is expected to grow significantly in the coming years, with rollout wheel welding being a key contributor. This growth is driven by increasing demand for high-performance wheels across various sectors, including automotive, aerospace, and construction. So yeah, this isn’t just a niche process; it’s a big deal!
- Bzbee Raw Honey The Sweetest Buzz In Town
- Ossa Collective A Revolutionary Movement Redefining Art And Community
A Brief History of Rollout Wheel Welding
Rollout wheel welding hasn’t been around forever, but its roots trace back to the early days of welding itself. Welding as a practice dates back thousands of years, with ancient civilizations using primitive methods to join metals. However, the modern rollout wheel welding process as we know it today started taking shape in the mid-20th century.
Back then, the focus was on improving the strength and durability of wheels used in vehicles and machinery. Engineers realized that traditional welding methods weren’t cutting it, especially for high-stress applications. That’s when rollout wheel welding stepped in, offering a solution that combined strength with aesthetics.
Over the years, advancements in technology have made this process even more efficient and precise. Today, we have computer-controlled machines and robotic arms that can perform rollout wheel welding with incredible accuracy. But hey, don’t let the tech fool you. At its core, it’s still about the skills and expertise of the welder.
The Rollout Wheel Welding Process
Step 1: Preparing the Materials
Before the welding begins, the materials need to be prepared. This involves cleaning the metal surfaces to remove any dirt, rust, or impurities. Think of it like washing your hands before a big meal. You want everything to be spotless to ensure a strong bond.
Step 2: Positioning the Components
Once the materials are ready, they’re positioned in the welding jig. This is where precision comes into play. The components need to be aligned perfectly to ensure a uniform weld. Any misalignment can lead to weak spots, so this step is crucial.
Step 3: Applying Heat
Now for the fun part – applying heat. The welding machine heats the metal parts to their melting point, creating a molten pool. This is where the magic happens. The metals fuse together, forming a seamless connection. It’s like melting chocolate and mixing it with peanut butter – you get something deliciously strong.
Step 4: Cooling and Finishing
After the welding is complete, the wheel is allowed to cool down gradually. This helps reduce stress and prevent cracking. Once cooled, the wheel is polished and finished to achieve that sleek, shiny look we all love.
Tools and Equipment Needed
Rollout wheel welding requires a few key tools and pieces of equipment. Here’s a quick rundown:
- Welding Machine – This is the heart of the operation. Modern machines come with advanced features like automatic temperature control and precision welding.
- Welding Jig – Used to hold the components in place during the welding process.
- Protective Gear – Safety first! Welders need protective clothing, gloves, and helmets to shield themselves from sparks and intense heat.
- Grinder – For smoothing out the weld and achieving a polished finish.
Having the right tools makes all the difference. It’s like trying to bake a cake without an oven – not gonna happen!
Benefits of Rollout Wheel Welding
So, why should you care about rollout wheel welding? Here are a few benefits that make it stand out:
- Strength and Durability: Wheels produced using this method are incredibly strong and can withstand heavy loads and high speeds.
- Aesthetic Appeal: The seamless finish makes them visually appealing, which is a big plus for the automotive industry.
- Cost-Effective: While the initial setup might be expensive, the long-term savings on maintenance and repairs make it a worthwhile investment.
- Versatility: Works with a wide range of materials and applications, making it suitable for various industries.
These benefits make rollout wheel welding a go-to choice for manufacturers and engineers alike.
Applications in Various Industries
Automotive Industry
Rollout wheel welding is a game-changer in the automotive world. From luxury cars to off-road vehicles, it’s used to create wheels that are both strong and stylish. Think about it – those fancy rims on sports cars? Yep, that’s rollout wheel welding at work.
Aerospace Industry
In the aerospace sector, strength and precision are non-negotiable. Rollout wheel welding is used to produce landing gear wheels that can handle the stress of takeoff and landing. It’s all about ensuring safety and reliability.
Construction Industry
Heavy machinery like bulldozers and cranes rely on durable wheels to get the job done. Rollout wheel welding ensures these wheels can withstand the toughest conditions, whether it’s a muddy construction site or a rocky terrain.
Tips for Successful Rollout Wheel Welding
If you’re new to rollout wheel welding or looking to improve your skills, here are a few tips to keep in mind:
- Practice Precision: Accuracy is key. Take your time to align the components properly before starting the welding process.
- Use Quality Materials: Don’t skimp on materials. Using high-quality metals will result in a stronger and more durable wheel.
- Invest in Good Equipment: Having the right tools can make your job easier and more efficient.
- Stay Safe: Always wear protective gear and follow safety guidelines to avoid accidents.
Remember, welding is as much about technique as it is about tools. Keep practicing, and you’ll be a pro in no time!
Common Challenges and Solutions
Like any process, rollout wheel welding has its challenges. Here are a few common ones and how to tackle them:
- Warpage: This happens when the metal distorts due to excessive heat. To prevent this, use controlled heating and cooling techniques.
- Porosity: Tiny holes or voids in the weld can weaken the connection. Ensure the metals are clean and free of impurities before welding.
- Inconsistent Welds: This can occur if the components aren’t aligned properly. Double-check your setup before starting.
Addressing these challenges will help you achieve better results and avoid costly mistakes.
Comparison with Other Welding Techniques
Rollout wheel welding isn’t the only game in town. There are other welding methods out there, each with its own pros and cons. Here’s a quick comparison:
- TIG Welding: Known for its precision, but slower and more labor-intensive.
- MIG Welding: Faster and easier to use, but may lack the finesse of rollout wheel welding.
- Laser Welding: Offers incredible accuracy, but is often more expensive and complex.
Each method has its place, but rollout wheel welding stands out for its balance of strength, precision, and cost-effectiveness.
The Future of Rollout Wheel Welding
As technology continues to evolve, so does rollout wheel welding. Innovations in robotics, artificial intelligence, and material science are pushing the boundaries of what’s possible. Imagine a future where wheels are produced with zero defects, using minimal energy and resources. Sounds pretty sweet, right?
Additionally, the focus on sustainability is driving the development of eco-friendly welding processes. Manufacturers are exploring ways to reduce waste and carbon emissions while maintaining quality. It’s an exciting time for the industry, and rollout wheel welding is at the forefront of this change.
Conclusion
Rollout wheel welding is more than just a process; it’s a vital part of modern manufacturing. From its humble beginnings to its current state-of-the-art applications, it has come a long way. Its ability to create strong, durable, and aesthetically pleasing wheels makes it indispensable across various industries.
So, whether you’re a seasoned professional or just starting out, there’s always something new to learn about rollout wheel welding. Dive in, experiment, and see where this fascinating field takes you. And hey, if you found this article helpful, don’t forget to share it with your friends and colleagues. Knowledge is power, after all!
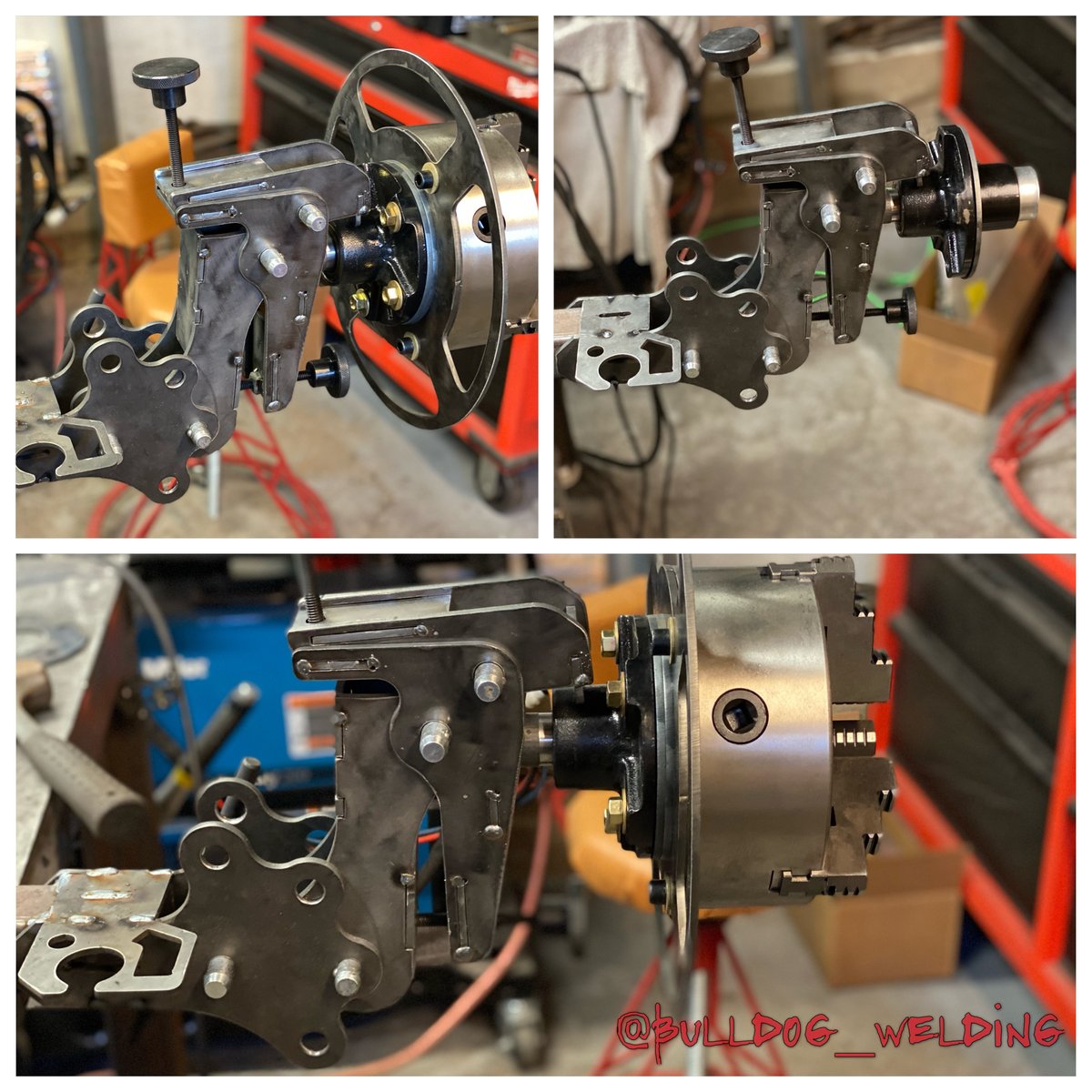

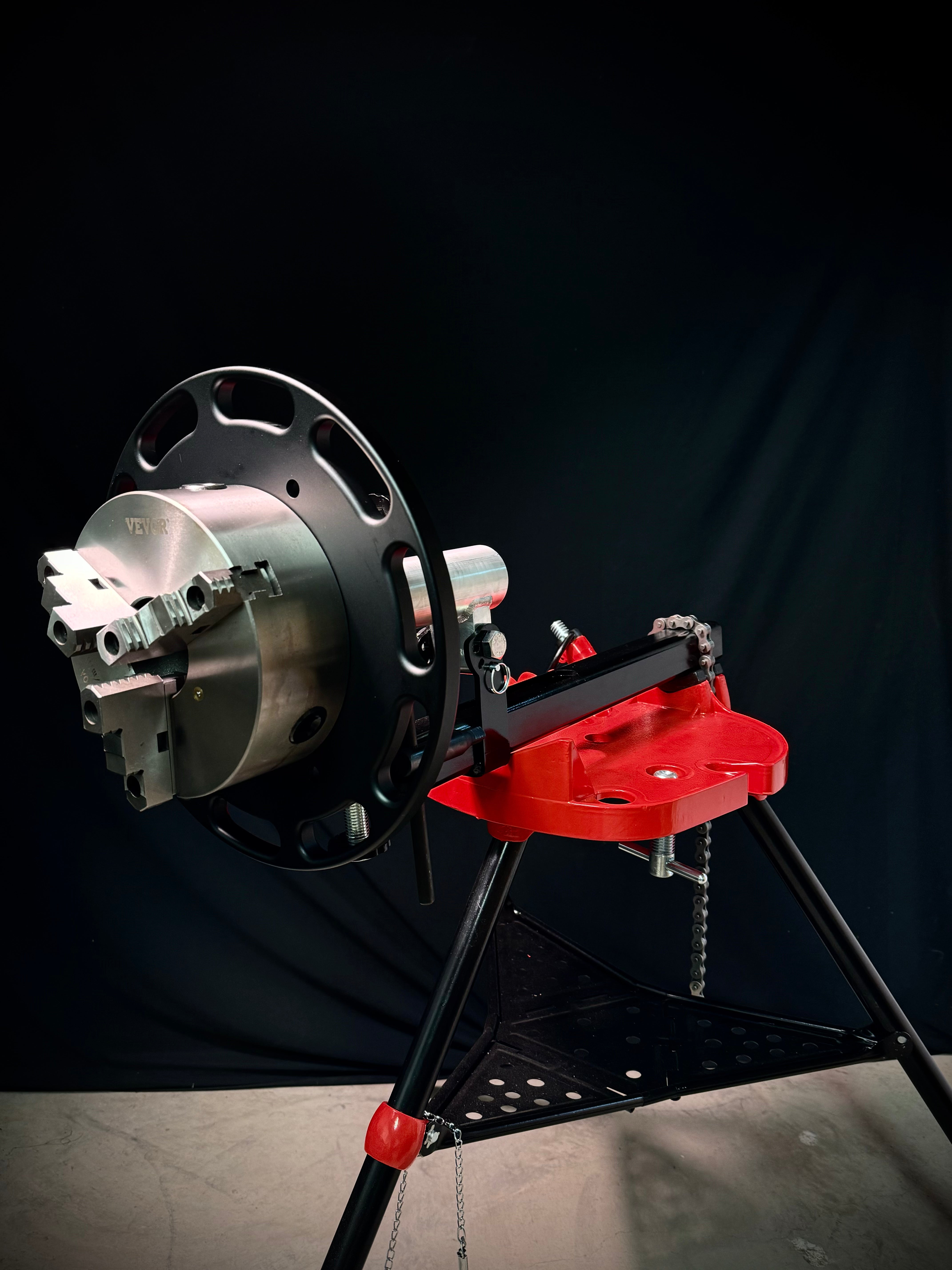